Today, beside the high volume of waste production and environmental concerns, the increasing demand and limited supply of primary resources in the field of production, has increased the importance of waste recycling. However, many of these disposable materials are reusable, which makes the recycling industry attractive to manufacturers.
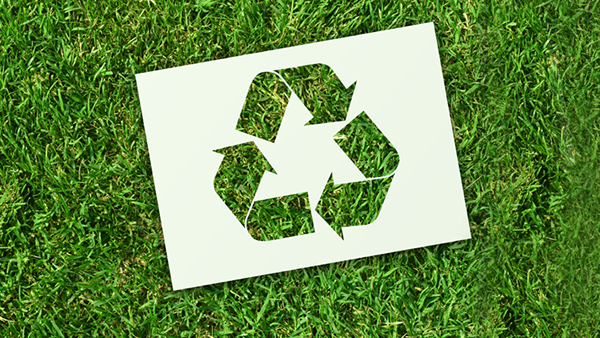
With the growth of production units, industrial waste has also increased. Many of these wastes that have made from recycled materials can be reused by the converting industries. Therefore, recycling lines, by converting these wastes into raw materials of other factories, has become one of the best ways to preserve the environment, save resources, maximize the use of raw materials and of course, be more profitable in production.
Garma Electric Company as the official representation of Andritz Denmark, imports the latest technology of this company in the field of recycling, launching factory lines and providing services in various parts of the recycling industry.
Andritz services in the recycling industry are included in the form of 8 separate solutions, which can be mentioned as follows:
1. Waste Electrical and Electronic Equipment (WEEE) and refrigerators
With the proliferation of electrical and electronic devices, Electronic scrap has become the fastest growing (estimated 50 million tons per year) waste stream in the world. With the potentially hazardous materials found in electronics, it is a challenge to break down and safely recycle components. A technical innovation from ANDRITZ Recycling – the ADuro QZ shredder – has made a big impact on successful E-scrap recycling operations.
Refrigerators, electrical and electronic components enter the Andritz recycling plant as raw materials. No cutting tools are employed in the shredder. The machine breaks down different composite materials quickly and gently using rotating chains so that the individual fractions (like iron, plastic, printed circuit boards, cables, and copper coils) are exposed and can be easily separated from one another in downstream processes. Components that contain hazardous substances, such as batteries and capacitors, remain intact and can be disposed of without any negative impact on the environment.
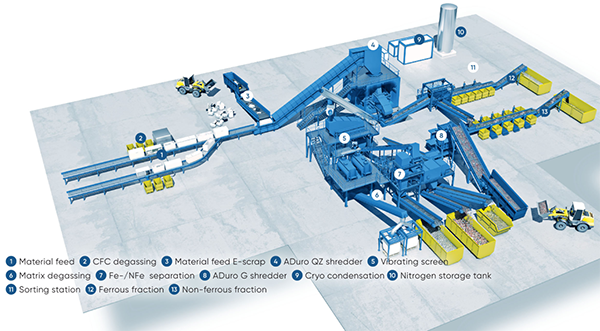
There are many different types of cables with a variety of material compounds: flexible wire cables, household cables, power cables, underground cables, copper and aluminum cables, and high voltage cables with V-PE sheaths.
Cable recycling and reusing these metals not only preserves and conserves valuable resources, it also significantly reduces energy consumption. It just requires a fraction of the energy that must be expended to initially mine and extract ore. In most cases, the individual materials in the cable or flexible wire adhere very closely to one another. To expose and process these fractions requires recycling technology that produces small grain sizes for optimum separation.
3. Metals Recycling and special processing
There are hundreds of different metal compounds containing components and materials which require specific processing technologies and methods to maximize their value and minimize environmental impact. Attractive and valuable metal compounds include ferrous fraction, aluminum, copper, or zinc because these materials can be sold as secondary raw materials and recycled multiple times without loss of quality.
Andritz special metal recycling technology with decades of experience called ANDRITZ MeWa, has the ability to separate all types of metals and raw materials from batteries, circuit boards, solar panels, cans, aerosol containers, mattresses, metal turnings, aluminum profiles, slags, scraps metal sheet, textile bales, or waste papers.
4. Vehicle parts and tires
Even at the end of their useful life, many of the components in an automobile or other vehicle, contain valuable raw materials, whether it is the metal in oil filters and precious metals in catalytic converters. The aluminum in wheel rims and engine blocks, or the pure rubber in used tires. ANDRITZ has the process technology and expertise to extract and reuse it. More recently, recycling technology has been developed for the growing number of lithium-ion batteries in electric cars.
For tires, this means breaking the used tire down into its main building blocks – rubber, steel wire, and textiles – so that these components can be recovered with highest purity in a three-stage process.
5. Substitute fuels and metal cleaning
Millions of tons of waste are produced in the world every day. While the main sources are the industrialized nations, the amount of waste is increasing in emerging economies as well. ANDRITZ employs technologies that combine pre-shredding, post-shredding, sorting, and drying so that the entire flow of waste can be separated into organic and inorganic components.
Valuable fractions, such as metals, can be removed early in the process and appropriately recycled. The metal fraction, often with plastics or textiles still adhering to it, can be cleaned. Composite materials can be broken down with the ADuro QZ shredder. In the end, the steel scrap and non-ferrous metals can be recovered with a superior purity of 98% – perfect for use in the steel industry or re-processing in foundries. Plastics, textiles, paper, PVC, metals, minerals, wood and glass are taken out of the factory as output and made available to consumers.
6. Pulp and Paper mill rejects
With very high recovery rates, wastepaper has become a very important raw material to substitute virgin fiber in the paper industry. However, the contaminants it contains (inks, glues, plastics, etc.) as well as metals and tying wires in the bales themselves must be removed and processed.
The ANDRITZ recycling portfolio includes innovative technologies for the processing of paper mill sludges and rejects, materials separation and recovery, and the generation of alternative energy sources to reduce a mill’s dependency on landfills, fossil fuels, and purchased power.
Perhaps the main advantage of this solution is the establishment of a paper recycling line in the paper factory itself, through which the manufacturer collects paper waste and recycles it, practically becoming independent in the production of its raw materials.
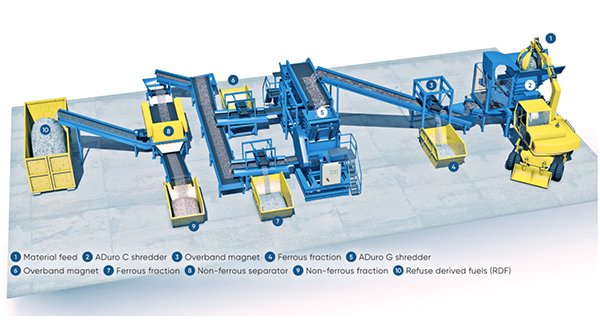
Potential wood waste markets include feedstock for composite materials, fuel for energy generation, animal bedding, and soil amendments. Due to the bulk, the recycled material is generally processed locally so that it does not have to be transported over long distances. The ADuro P and ADuro U shredders are superior multi-talents at work and handle bulky wood waste inputs easily.
Wood wastes such as offcuts, veneers, boards from demolition projects, construction sites, and timber processing operations can be effectively processed with ANDRITZ shredding technology. The slowly rotating ADuro P and ADuro U shredders can process large quantities of wood and even huge logs into manageable sizes (10 to 200 mm). The output size is determined by the screen choice.
Benefits:
• High-capacity throughput (up to 50 t/h)
• Large inlet hopper
• Dependable, innovative continuous cutting system
• Insensitive to impurities and contaminants
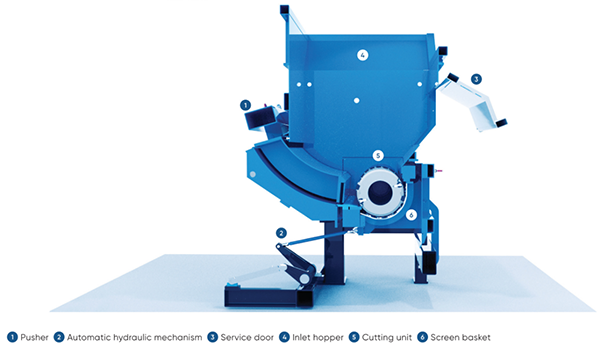
The increasing growth of the human population has increased the consumption of food and organic materials with a very steep slope, and this has led to the production of large volumes of waste and natural wastes; therefor ANDRITZ has developed a special ADuro QZ system to prepare packaged foods, organic waste, and energy crops for optimum fermenting conditions in biogas plants.
The ADuro QZ shredder breaks down the cell structure of input waste materials (e.g. organic waste, corn and whole crop silage, grass silage, farmyard manure, restaurant and kitchen waste, and packaged foods) to maximize the contact surface area for fermentation bacteria to perform their magic. Biogas formation begins measurably faster and more intensely, which can reduce the duration of the fermentation process substantially. This, in combination with significant yield improvement, boosts the cost-effectiveness of a biogas plant.
A major advantage of the ADuro QZ is its ability to separate organic materials from food packaging by crushing and stirring the material in one process. The output is unwrapped organic waste, suitable for pumping. After the organic materials are removed, the packaging and other inorganic components can be easily separated out.
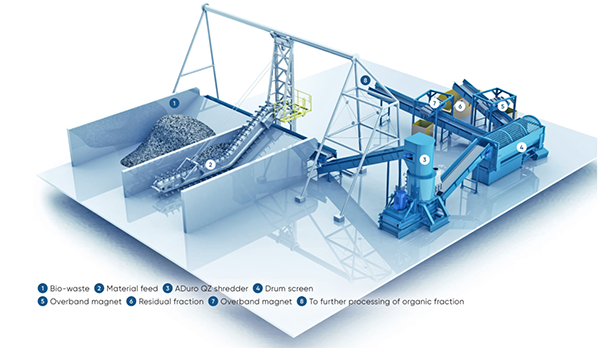