Although Vacuum Coaters have been developed for producing aqua feed and pet food, they have been widely used to produce poultry feed that is larger in size in recent years. But the question is what is the goal or in the other words, the need to justify for using of high technology such as Vacuum Coater. Here are some of the main reasons for this necessity:
1-High temperature in some feed production processes
In modern animal feed manufacturing methods, processes are used that lead to increase material temperature during production. Conditioning is one of the most important processes that is increasing the temperature of materials, which is almost common in pellet and extruder solutions, can be mentioned. In this process, adding hot steam leads to increase temperature. Other processes such as the passage of feed through the pellet die or via the extruder, grinding and expanding also greatly increase the temperature of the raw materials.
Other heat-sensitive materials include flavors and colors, which are especially important for producing pet food. One of the reasons for the difference in quality of the products of famous pet food brands compared to other manufacturers is that they are using this technology.
The high temperature, beside the advantages like health or producing feed with a more appropriate appearance, damages some useful nutrients such as vitamins or enzymes and etc. Because of this action, quality of final feed is reduced.
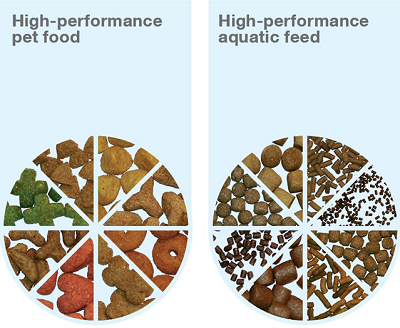
2-Restriction on adding liquids containing micronutrients, especially fat/oil in the formula
In addition to the above points about the effects of high temperatures, there is another limitation for nutritionists, the maximum fat in formula. One of the main features of proper design and selection of equipment, is to create flexibility for nutritionists as much as possible; so, they can produce products more easily with the highest quality from the available raw materials.
In pellet press and extruder solution, there is a serious limitation for maximum percentage of fat/oil in formula. For example, if the fat content is high, the capacity and performance of the hammer mill will be disrupted. If we add fat/oil to the ingredients in the mixer, it is not possible to produce high quality feed in pellet machine and especially the extruder at high fat percentages. (in advanced technologies, maximum possible use percentage, is higher). Increasing in fat, leads to decrease the pressure inside extruder which causes a serious disturbance in the general idea of extrusion, which is based on the difference between the extreme pressure inside and outside.
3-Inserting materials into the seeds
In addition to above, dietitians may be interested in adding liquids inside the feed and impregnating the outer surface with the least amount of added fluid. Implement this requirement is quite understandable given the way of aquatic feed; It is impossible with the old method of coating which is done under normal air pressure.

as a result, vacuum coating technology offers high flexibility to nutritionists and can lead to further production chain optimization.
How vacuum coaters work:
The simplified process of vacuum coating includes the following steps:
- Ingredients enter the vacuum coater
- Creating a vacuum, appropriate to the type of vacuum coater
- Measuring and spraying liquids on feed
- Bringing air back into the system
- Fluid enters the feed along return air
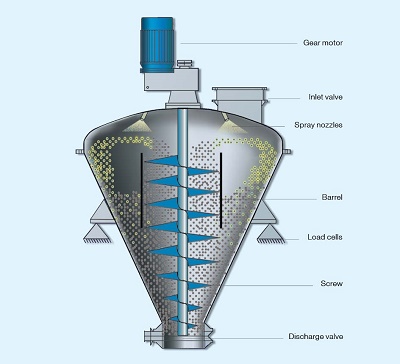
Here is a brief description of the Andritz vacuum coaters:
In the VAC Andritz vacuum coaters series, the materials are gently moved by a vertical screw after entering a conical tank. Extruded pellets have a very porous inner structure. The objective of vacuum coating is to use a pressure differential to force liquids through the outer layer and deeply into the porous area of the pellet. The suction system drains the air inside the grains and then the liquids, powders, nutrients and dyes are sprayed 360 degrees and evenly.
Vacuum pressure should be controlled according to the volume of fluid added. To have a high level of coverage, a longer release time (often up to 180 seconds) is required.
In Figure 1, the release time of the short pressure is 30 seconds: air enters the product and therefore has an adverse absorption property.
In Figure 2, the release time of the long pressure is 180 seconds: it causes the liquids to enter the center of the product slowly.
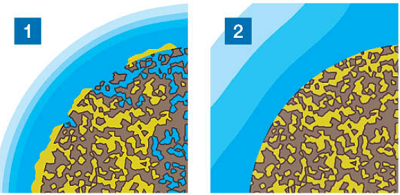
The ANDRITZ vacuum coating system provides accurate control of vacuum pressure, liquid addition and cycle time to allow flexibility and repeatability in terms of degree of absorption and penetration.
Advantages of using Andritz vacuum coaters:
• Capable of addition up to 15 individual liquids.
• The low-energy input of vertical units assures that mixing occurs without shear.
• Using a vertical-transport screw allows all products to be exposed over time at the top of the mixing vessel, which provides the ideal medium for the uniform application of liquids or powders.
• Comes with or without vacuum.
• Add high amounts of liquids up to 35% of dry matter weight (up to 45% if using Andritz ECS system)
• High spray efficiency (for example, liquids in very small volumes)
• Vacuum pressure up to 10 mL
• High flexibility for production with different capacities and batch
Click Here for more Details.