Reducing the temperature and cooling is one of the important indicators in the feed production process, which has a significant contribution in increasing the pellet durability index (PDI) and hygiene of the product. This is done for reducing the heat and moisture of the produced feed, with the help of cooling machines called cooler.
The input of this device is:
- The product produced (output from the pellet mill or extruder) which is hot and wet
- Ambient air
The output is feed pellet with specified level of moisture (country specific), temperature and pellet durability index (PDI). This moisture, if remains in the feed, can reduce PDI (Pellet Durability Index), which in addition to reducing the quality, making it very difficult to storage and maintenance.
In the past, these devices were produced only in the horizontal type (Horizontal Cooler), but today, a more advanced type of them is marketed as the Counter-flow Cooler.
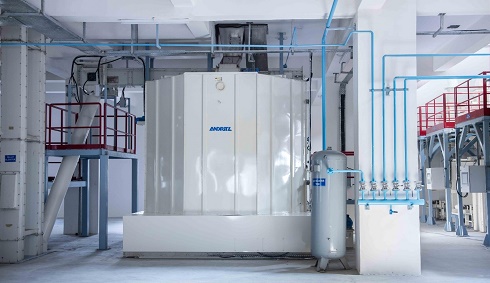
The basis of the cooler is the passage of ambient air flow through the pellet feed in order to remove the added moisture in the previous steps; Therefore, by placing the cooler in the production path, the feed taken out of the press pellet or extruder is spread inside it so that by blowing air into the chamber, heat and humidity of the product are taken thus dry and suitable pellets are prepared.
Garma Electric, as the official representative of Andritz, imports and services the company's products, including Counter-flow Cooler. The vertical cooler is suitable for optimum cooling of extruded or pelletized products based on customer applications and preferences. It prepares the pellets optimally for storage and is one of the cleanest solutions due its discharge system.
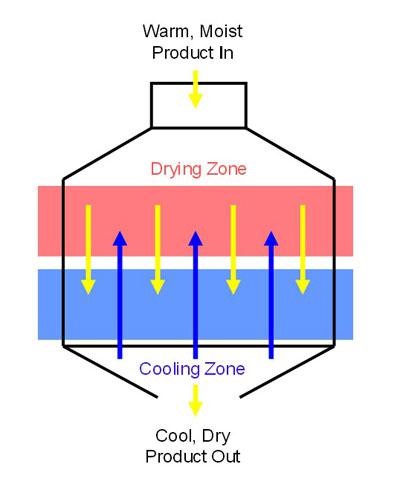
Since the ambient temperature is lower than the product temperature, the heat transfer operation takes place and the feed is cooled. During this air passage, moisture is also released from the material.
This process continues continuously, and new pellets enter the device from the upper inlet of the chamber and follow the top-down path, while the air flows from the bottom to the top. Due to the reverse flow of these two paths, this device is called Counter Flow cooler.
Among the advantages of this device are the following:
- Reduce product temperature from 85 ° C to a maximum of 5 ° C more than ambient temperature
- Cooling of produced materials to facilitate storage and increase storage time
- Provide proper energy transfer
- Low maintenance and operation costs of the device
Click Here for the Details